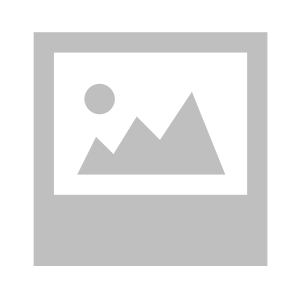
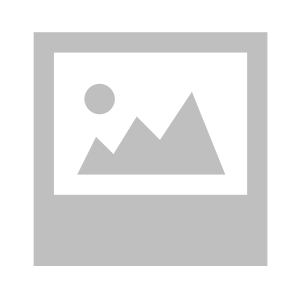
نت بهرهور TPM :از زمانیکه اولین اسناد در زمینه سیستم نت بهرهور جامع (TPM) ارائه گردید. بیش از سی سال میگذرد. نگهداری و تعمیرات فراگیر اولینبار در کشور ژاپن توسعه یافت. این سیستم توسط شرکت Nippon Enson که تولیدکنندهی قطعات یدکی اتومبیل است بطور رسمی در سال 1971 اجرا شد. نسخه اول سیستم TPM به مدل Nakajima (از بنیانگذاران TPM) مشهور بوده و تا سال 1989 نیز در اصول پنجگانه آن تغییری داده شد. با تغییر نگرش در سیاست های کلان TPM، ویرایش دوم و سوم سیستم مذکور (در طول سالهای 1989 الی 1994) توسط آقای T.Suzuki ارائه گردید که یکی از ویژگیهای مهم ویرایش سوم افزایش اصول سیستم به هشت اصل (به شرح زیر) میباشد :1- افزایش میزان اثز بخشی کلی ماشینآلات2- اجرای نت خود کنترلی توسط پرسنل خطوط3- اجرای نت برنامهریزی شده توسط بخش نگهداری و تعمیرات4- برگزاری دورههای آموزشی تئوری و عملی برای کلیه پرسنل5- مدیریت زود هنگام بر روی ماشینآلات6- استقرار سیستم نت کیفیتی با ایجاد ارتباط بین واحدهای نت و کنترل کیفیت7- استقرار نت بهرهور فراگیر در واحدهای پشتیبانی و ستادی نت8- مدیریت ایمنی محیط زیستTPM (Total Productive Maintenance) یا نگهداری – تعمیرات بهرهور فراگیر میباشد. هدف TPM بنای تشکیلاتی است نیرومند جهت سیدن به حداکثر راندمان در سیستم تولید. TPM کل چرخه سیستم تولید را هدایت کرده، سیستمی واقعی بر مبنای اطلاعات سطح کارخانه ایجاد میکند. تا از کلیه اتلافات جلوگیری کند.مدیریت نگهداری و تعمیرات :مدیریت نگهداری و تعمیرات، فرایندی است که سبب تحقق اهداف یک سازمان میشود، با توجه به این تعریف، مدیریت نت شامل فعالیتهای مهمی مانند هدفگذاری، تعیین استراتژی، سازماندهی، برنامهریزی، استانداردسازی، کنترل منابع، نظارت بر اجرای برنامهها، ایجاد تعهد و انگیزه در کارکنان، ایجاد رقابت سالم و فراهم نمودن محیطی سرشار از تفاهم، همدلی و همکاری است. تا سازمان نت بتواند به اهداف تعیین شده دست یابد.TPM دارای 5 مشخصه میباشد :الف) بیشینه کردن کارایی تجهیزاتب) استقرار یک سیستم فراگیر نت پیشگیرانه (PM)ج) در بر گرفتن کلیه افراد مرتبط با تجهیزاتد) مشارکت همگانی از مدیریت عالی شرکت تا کارکنان خط تولیده) نت پیشگیرانه خودکار در قالب فعالیتهای گروههای کوچکاهداف فعالیتهای گروههای TPMهدف TPM، بیشینه کردن کارایی تجهیزات و حذف شش ضایعه بزرگ شامل خرابیهای اضطراری آمادهسازیها و تنظیمات، توقعات جزئی، کاهشسرعت و ضایعات کیفی در ابتدای راهاندازی و در طول فرایند میباشد. همه اینها سبب بهبود عملکرد شرکت و ایجاد محیط کار سالم میگردد.سازماندهی گروههای TPM به صورت همپوشانیدر TPM سطوح مختلفی از گروهها تشکیل میشود. مانند گروه مدیران، گروه سرپرستان و گروه کارگران خط تولید. این گروهها به صورت زیر همپوشانی دارند که آن را سازماندهی همپوشانی گروهها میگویند.میتوان نگهداری – تعمیرات را ا زمان ظهور آن در سال 1930 میلادی تاکنون و در قالب سه دوره متوالی بررسی کرد.دوره اول از سال 1930 تا قبل از آغاز جنگ جهانی دوم میباشد. در آن زمان صنعت به صورت به صورت کنونی مکانیزه نبود، و لذا زمان توقف دستگاهها زیاد اهمیتی نداشت.نسل دوم : در جریان جنگ جهانی تغییرات بسیاری در جهان به وقوع پیوست. فشارها و شرایط ناشی از جنگ باعث ایجاد تقاضای زیاد انواع کالا شد، در حالیکه قدرت تولید این کالاها به شدت کاهش یافته بود. این شرایط جدید باعث شد مکانیزاسیون در صنعت گسترش یابد، به طوریکه در آغاز دهه 1950 ماشینهای زیاد و پیچیدهای در صنعت به کار گرفته شده بودند.نسل سوم : بعد از دوره دوم جهش صنعتی در تکنولوژی نت، افزایش میزان پیچیدگی و گسترش سازمانها و منابع آنها و افزایش هزینههای نگهداری – تعمیرات منابع فیزیکی منجر به کنکاش روشهایی جهت افزایش عمر مفید ماشینآلات و تجهیزات شد.بررسی ارکان هشتگانه TPMTPM - رکن اول 5S : TPM با 5S شروع میشود. وقتی محیط کار تمیز نباشد مشکلات به خوبی شناخته نمیشوند.TPM – رکن دوم : نت خود کنترلی : این رکن اپراتورهای را آماده میکند تا بتوانند فعالیتهای ساده نگهداری و تعمیرات را انجام دهند.TPM - رکن سوم : کایزن : کایزن یک ترکیب ژاپنی است که از دو کلمه "Kai" به معنی تغییر و "zen" به معنی خوب (برای بهتر شدن) تشکیل شده است. اساساً کایزن برای بهبودهای کوچک ولی به صورت مستمر و با مشارکت کلیه افراد سازمان است.TPM - رکن چهارم : نت برنامهریزی شده : این رکن به دنبال داشتن تجهیزاتی سالم و تولیدی بیعیب برای جلب رضایت مشتری است. در اینجا فعالیتهای نت را به چهار دسته اساسی تقسیم میکنیم : تعمیرات پیش بینی شده، تعمیرات اضطراری ، تعمیرات اصلاحی ،پیشبینی تعمیراتTPM - رکن پنجم : حفظ کیفیت : هدف این رکن کسب رضایت مشتری نهایی با تحویل با کیفیتترین محصول در خلال ایجاد کارخانهای بیعیب و نقص است. TPM - رکن ششم : آموزش : هدف داشتن پرسنلی چند مهارتهای است که با شور و علاقه وظایف خود را به نحو احسن انجام دهند.رکن هفتم : TPM اداری : هدف افزایش بهرهوری و کارایی در فعالیتهای مدیریتی و ستادی است. تحلیل فعالیتها، افزایش سطح اتوماسیون کارهای اداری از مهمترین کارها در این رکن است.TPM - رکن هشتم : ایمنی و سلامت محیط زیست : اهداف : حذف حوادث ، حذف خسارات جانی ، عدم آتشسوزی .آشنایی با مفهوم در TPMدر اینجا با آشنا میشویم و آن همان شش ضایعه بزرگ ناشی از تجهیزات در صنعت است که حذف آنها یکی از ارکان اجرای TPM است. اینشش ضایعه عبارتند از :ضایعه ناشی از تلفات شروع تولید مجدد ، ضایعه ناشی از توقفات و خرابیهی طولانی مدت ، ضایعه ناشی از تنظیم مجدد و راهاندازی دستگاه ضایعه ناشی از کاهش سرعت و ظرفیت دستگاه ، ضایعه ناشی از توقفات کوتاه مدت و انقطاع تولید ، ضایعه ناشی از تولید نامرغوب به علت خرابی تجهیزنقش مدیران و سرپرستان در ایجاد سه وضعیت :مدیران و سرپرستان بایستی این شرایط را ایجاد کنند : خواستن ، توانستن و محیط کاریگروهها چگونه شکل میگیرند ؟ گروههای TPM به عنوان بخشی از شرکت به شمار میروند. هر گروه متشکل از 5 تا 10 نفر عضو، مسئول یک تجهیز معین میباشد. سرپرستان نیز عضو این گروهها هستند.چگونه سرگروه انتخاب میشود؟ سرگروه باید دارای فناوری و دانش توسعه یافته راجع به سازمان باشد و نیز آگاهیهای کیفیتی، روشهای بهبود و قدرت رهبری توانمند داشته باشد.معمولاً ، سرپرستان به عنوان سرگروه انتخاب میشوند.هر عضو یک قهرمان فعالیتهاستبرای یافتن خرابیهای پنهان، هر کس باید تجیزات را با شناخت و آگاهی کامل به کار گیرد. هر یک از اعضای گروهTPM بایستی این دیدگاه را داشته باشد : "من خودم تجهیزاتم را بهتر از همه میشناسم، من خودم مواظب تجهیزات خودم هستم و این وظیفه من است که تجهیزات را کنترل کرده "چگونه مسائل را تشخیص دهیم ؟الف- به ضایعات، ناپایداریها و نامعقولات توجه کنیدب- شش ضایعه بزرگ تجهیزات1- ضایعات خرابیهای اضطراری : خرابیهای ناگهانی و مزمن باعث تلف شدن زمان (نسبت به تولید) و تلف شدن مواد (ضایعات محصول) میشود.2- ضایعات آمادهسازی و تنظیم : این ضایعات عبارت است از زمان تلف شده بین انتهای یک جریان تولید و شروع جریان بعدی تولید، وقتی که ماشینآلات برای تعویض یا تنظیم مجدد قالبها و اتصالات متوقف شدهاند.3- ضایعات حرکت بدون تولید و توقفات جزئی : این ضایعات وقتی به وجود میآیند که تجهیزات به دلیل عوامل بیرونی متوقف شدهاند یا وقتی که آنها در حال حرکت و کار بدون تولید هستند.4- ضایعات کاهش سرعت : این ضایعات ناشی از اختلاف بین سرعت طراحی شده و سرعت واقعی بهرهبرداری است. نشانههای آن عبارتند از : محصولات و مواد با مشخصات متفاوت ، مشکلات ماشینها یا محصولات ، نامعلوم بودن سرعت طراحی شده ماشین5- ضایعات محصول در فرایند و دوبارهکاریها : این ضایعات شامل ضایعات مواد (کاهش تولید و توقف) و ضایعات نفر – ساعت (زمان صرف شده برای اصلاح محصولات معیوب) میباشد.6- ضایعات آغاز تولید و زمان راهاندازی : این ضایعه مربوط است به زمانی که برای تولید محصول جدید راهاندازی صورت میگیرد تا زمانی که تولیدبه حالت پایدار و مورد نظر میرسد.محیط کارتان را بهبود بخشیدالف- با 5S (با سازماندهی محیط کار) شروع کنید. مشخص شدن واضح مسایل و مشکلات، گام نخست به شمار میآید و این مستلزم وجود یک محیط کار مرتب است. 5S را به کار ببرید. Seiri تفکیک، Seiton ترتیب، Seiso تمیزی، Seiketsu تداوم و استانداردسازی و Shitsuke تربیت و انضباط.ب- فضایی به وجود آورید که بحث در آن راحت باشد و هر کس بتواند در آن صحبت کند و آزادانه نظرات خود را ابراز نماید.ج- اتاق جلسه مهیا کنید.دیوارهای اتاق را به گواهینامهها و لوحهای موفقیتهایی که به دست آوردهاید تزئین کنید.تقویت رهبریالف- رغبت و رضایت خاطر سرگروه : این موضوع، باعث ارتقای روحیه، فعالیتهای بیشتر و موفقیتهای بزرگتر می گردد.ب- شش شرط برای سرگروه :به فعالیتهای گروه اشتیاق و علاقه داشته باشد ، به عقاید اعضای گروه احترام بگذارد ، قادر باشد تا افراد را به ابراز عقایدشان ترغیب کند ، در خود آموزشی پیشقدم باشید ، برای بهبود فعالیتهای گروهی، تلاش و از خود گذشتگی داشته باشد ، یک سرگروه خوب، رغبت و رضایتخاطر اعضاینمودارها : نمودارها، ماند نمودارهای خطی یا میلهای، هر کس می تواند که در یک نگاه، وضعیت کنترل را مشاهده کند.نمودار پارتو : دادهها را بر مبنای نوع علتهای آنها دستهبندی و به ترتیب نزولی مرتب کنید. میلههای عمودی که به ترتیب نزولی مرتب شدهاند میزان فراوانی هر علت را نشان میدهند. خطی که در بالای میلهها کشیده شده، بیانگر منحنی درصد تجمعی دادههاست.نمودار علت و معلول : این نمودار نشان میدهد که چگونه علت و معلول به هم ربط پیدا میکند.برگه کنترل : برگه کنترل دادههای دستهبندی شده را ثبت میکند و از ان برای تعریف مسئله با دسترسی به دادههای سازمان یافته، به عنوان یک منبع برای ارزیابی و تعیین روند و چگونگی توزیع مسائل استفاده میشود.نمودار کنترل : نمودار کنترل برای کشف موارد غیر طبیعی فرایندها به کار میرود. علیرغم استفاده از فرایند و مواد مشابه، اختلافهایی در محصولات نهایی به چشم میخورد که این اختلافات میتواند قابل چشمپوشی (طبیعی) و یا غیر قابل چشمپوشی (غیرطبیعی) باشد و این را با مقایسه دادهها با خطوط محدوده کنترل میتوان نتیجه گرفت. حرکت نقاط (روندها) نشان میدهند که آیا فراید پایدار است یا ناپایدار؟طبقهبندی :طبقهبندی یعنی دستهبندی کردن دادهها بر مبنای مشخصات آنها، و اگر به خوبی انجام شود به شما این امکان را میدهد تا علل و نیز مؤثرترین علت را شناسائی کنید.آنالیز PM : آنالیز PM، روشی است که به شما کمک میکند تا اقدامات متقابلی را که بکار میگیرید با توجه به تمامی عواملی باشد که شما میتوانید راجع به آنها فکر کنید و این شامل آنالیز فیزیکی نیز میگردد.مهندسی ارزش (VE) : مهندسی ارزش، فنون هزینه مداری را برای توسعه و بهبود کارکردها به کار میگیرد و آن را آنالیر ارزش نیز میگویند. درباره کارکردها و بهبودها با توجه به نکات زیر بیندیشید : چرا ما این کار را میکنیم؟ چرا این چیز، اینجاست؟ آیا روشهای دیگری وجود دارد؟ ارزانترین روش کدام است؟مهندسی صنایع (IE)مهندسی صنایع به دنبال حذف ضایعات، ناپایداریها و نامعقولات است. شما باید :الف- حرکت و گردش کارگران را همراه با جزئیات آن آنالیز کنید.ب- حرکت و گردش کالاها را همراه با جزئیات آن آنالیز کنید.مهندسی صنایع از زمانسنجی، آنالیز رفتار و نمودارهای جریان کار استفاده میکند.....مهندس ایمان اجری پور


یک نظر اضافه کنید
شماره موبایل شما منتشر نخواهد شد.زمینه های مورد نیاز هستند علامت گذاری شده *
امتیاز شما