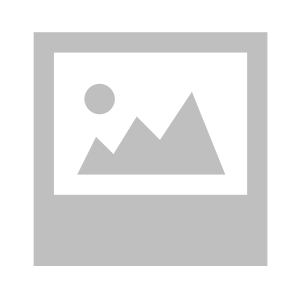
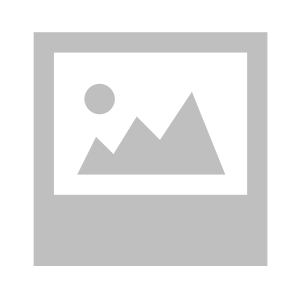
چکیده: هر سال واژههای جدیدی در عرصه کیفیت و بهرهوری متولد میشوند واژههایی که برخی اشاره به بنیانهای این علم داشته و برخی صرفا پرطمطراق و دهان پرکن، جنبه تبلیغاتی برای شرکتهای مشاوره مدیریت دارند. در این بین اغلب مدیران ایرانی، غافل از تقدم/تاخر و چیستی این سیستمهای مدیریتی، یکی را برای دستیابی به کیفیت و بهرهوری برتر بر میگزینند تا شاید وصال مقصود حاصل شود! در این مقاله سعی خواهد شد اولین و مهمترین گام در این مسیر از نظر اساتید مدیریت معرفی گردد.
لغات کلیدی: سیستمهای برتر کیفیت و بهرهوری، بهبود مستمر، تولید بهنگام، تولید ناب، نظام پیشنهادها
مقدمه:
شناسایی و حذف همه فعالیتهای فاقد ارزش افزوده و افزایش ارزش افزوده سایر فعالیتها از مرحله تهیه مواد اولیه تا تولید و نهایتا فروش، هدف غایی تمامی سیستمهای ارتقاء کیفیت و بهرهوری شامل تولید بهنگام، تولید کاملا بی نقص، تولید ناب و... میباشد ولی برخی از سازمانها ابزار اصلی برای دستیابی به این هدف را گم کرده و سر از ناکجاآباد در میآورند.
برای مثال در اجرای تولید بهنگام یکی از اهداف مهم، حذف همه موجودیهای مواد اولیه، نیمه ساخته و محصول میباشد. موجودیهایی که قسمت اعظم آن به خاطر ناکارآمدی زنجیره تولید نگهداری میشوند. مثلا ذخیره اطمینان(safety stock) مواد اولیه به خاطر احتمال تاخیر در دریافت مواد اولیه در نظر گرفته شده است که مسلما اگر تامین کننده (Supplier)از قابلیت اطمینان بالایی برخوردار باشد به طوری که احتمال تاخیرش به صفر میل کند نگهداری ذخیره اطمینان مواد اولیه، عقلایی و به صرفه نخواهد بود.
یا به خاطر احتمال خرابی ناگهانی هر یک از دستگاههای خط تولید که منجر به توقف تولید خواهد شد اقدام به نگهداری موجودی نیمه ساخته از محصول هر یک از دستگاهها میگردد. همین طور به خاطر ناکارآمدی واحد فروش در پیش بینی تقاضای بازار، موجودی کالای ساخته شده در انبار نگهداری میشود.
در اجرای تولید بهنگام، گام به گام اقدام به حذف این موجودیها میگردد تا ناکارآمدی بخشهای مختلف نمایان شود و واحدهای مختلف به اصلاح عملکرد خویش بپردازند ولی اگر به معنای واقعی همه بخشهای سازمان برای حذف این ناکارآمدیها و بهبود امور تلاش نکنند حذف موجودیها نه تنها هیچ سودی ندارد بلکه باعث بوجود آمدن مشکلاتی بس عظیمتر خواهد شد. برای مثال خرابی یک دستگاه در خط مونتاژ باعث توقف خط تولید، افزایش هزینههای تولید، فشار بر کارکنان و دستگاهها، تاخیر در تحویل محصول به مشتری و از دست رفتن اعتبار شرکت، کاهش سفارشات دریافتی و... خواهد شد و به این ترتیب به معنای واقعی، سازمان خود را در ناکجاآباد گرفتاریهای مضاعف تولید بهنگام خواهد دید! با پیگیریهای بعدی مشخص خواهد شد خرابی دستگاه به خاطر نگهداری-تعمیرات نادرست دستگاه بوده البته نه به خاطر ضعف یا مسئولیت ناشناسی واحد نگهداری-تعمیرات بلکه به دلیل عدم تامین بموقع بودجه خرید قطعات یدکی که البته نه به خاطر ضعف واحد مالی بلکه به دلیل تخصیص دیرهنگام بودجه واحدهای مختلف که البته نه به خاطر ضعف مدیریت مالی بلکه به دلیل درگیر بودن ایشان در مشکلات تجدید ساختار سازمانی که البته نه به خاطر..... و این رشته سر دراز دارد تا جایی که بعضا چرخش نامناسب کواکب (!) هم به یکی از دلایل بروز مشکل بدل میشود.
واقعیت این است که به واسطه ماهیت سیستمی سازمان و تعامل اجزا با یکدیگر، نه تنها برای دستیابی به اهداف تولید بهنگام بلکه برای دستیابی به هر هدفی در زمینه بهبود کیفیت و بهرهوری مثل نزدیک شدن به دوباره کاری و ضایعات صفر، زمان آمادهسازی صفر، حمل و نقل و زمان تدارک صفر(Lead Time)، خواست و مشارکت همه اجزای سازمان امری ضروری است.
ابزار اصلی برای دستیابی به کیفیت و بهرهوری برتر کدام است؟
شاید برای بسیاری از مدیران باهوش و متفکر این سوال پیش آمده باشد که هسته اصلی سیستم تولید تویوتا، تاثیرگذارترین سیستم تولید در چند دهه اخیر، سیستم تولیدی که بسیاری از مفاهیم نوین در زمینه کیفیت و بهرهوری همچون تولید بهنگام(JIT: just in time) ، مدیریت کیفیت فراگیر (TQM: Total quality management)، کانبان (Kanban) ، تولید کاملا بی نقص (Zero defect) ، تولید ناب (lean production)، خطا ناپذیرسازی (Mistake proofing: poka yoke) ،SMED (Single digit Minute Exchange of Dies) و... از درون آن متولد گشتهاند چیست؟
دکتر شینگو (Shigeo shingo) یکی از افراد مهم در تحول شرکت به تویوتای برتر امروزی در آغاز فصل 5 کتاب "سیستم مدیریت تولید تویوتا" که کتاب مرجع در زمینه تولید ناب و بهنگام به حساب میآید این سوال مهم را مطرح میکند که واقعاً «سیستم تولید تویوتا چیست؟» در پاسخ مینویسد: « وقتی این سوال مطرح میشود 80% افراد میگویند "همان سیستم کانبان است" ، 15% دیگر با اطلاع از عملکرد آن ممکن است بگویند "یک سیستم تولیدی است" و فقط 5% واقعاً از هدف آن اطلاع دارند و میگویند «سیستمی است برای حذف کامل همه موارد زائد و غیر ضروری». در ادامه مینویسد: «برخی تصور میکنند تویوتا مجموعهای از لباسهای زیبا در اختیار دارد لذا سعی میکنند همان لباسها را بخرند و بپوشند. آنها خیلی سریع در مییابند که خیلی چاقتر از آن هستند که بتوانند چنین لباسی بپوشند! قبل از آنکه کانبان بتواند فایدهای برای آنها داشته باشد باید بتوانند موارد غیر ضرور را حذف و بهبودهای اساسی در سیستم تولید خودشان ایجاد کنند. 80% سیستم تولید تویوتا را حذف زوائد، 15% آن سیستم تولید و فقط 5% آن از کانبان تشکیل میشود.»
اما تنها راهکار حذف زوائد تا داشتن سیستمی بهرهور و با کیفیت در تولید، "بهبود مستمر با مشارکت تمامی کارکنان" است. این واقعیت به روشنی در توضیحات رابینسون و شرودر (2004، 173) درباره اجرای تولید بهنگام در تویوتا نمایان است: «با هدف قرار دادن تولید بهنگام سازمان مجبور بود به جزئیات بیش از حد متداول توجه نشان دهد و مدیران نیز به تنهایی نمیتوانستند برای همه مشکلات ریز و درشت سازمان راه حل ارائه دهند پس سازمان مجبور بود از همه کارکنان خط تولید کمک بگیرد و نهایتا در تویوتا یک سیستم ایدهسازی بسیار فعال بوجود آمد...» به نظر چنگ (Cheng) (1996، 8) نیز «بهبود مستمر یک بخش جداییناپذیر از مفهوم تولید بهنگام میباشد و برای اینکه موثر باشد باید بوسیله تمامی اعضای سازمان پذیرفته شود نه اینکه فقط کسانی که مستقیما در فرآیندهای تولید درگیرند آن را بپذیرند.»
همین طور در مورد تولید ناب بودک (Bodek) (2006) معتقد است: «مهمترین چالش پیش روی سازمانها در تبدیل شدن به سازمانی ناب، بوجود آوردن عادت بهبود مستمر در کارکنان میباشد.» پیتل (Patel) (2005،27) در مورد مدیریت کیفیت فراگیر معتقد است: « لغت فراگیر (Total)معنای متفاوتی در مدیریت کیفیت فراگیر دارد و آن درگیر شدن همه افراد سازمان از مدیر عامل تا پایینترین سطح کارکنان میباشد.»
در واقع «در دنیای امروز که رقابت بسیار سخت و خشنی بین شرکتها وجود دارد و فاصله شرکتها هر روز کمتر و کمتر میشود بهبود پایدار به امری حیاتی برای شرکتها تبدیل شده است. این بدین معناست که باید یکی از ویژگیهای کلیدی و اساسی کسب و کارمان بهبود مستمر باشد.» (Herriot & Stickland 1997 ، 607) «در این دوران بهبود مستمر در تمامی جنبههای کسب و کار به امری ضروری برای غلبه بر چالشهای ناشی از محیط پر تلاطم تجارت تبدیل شده است.» ( Bessant & Caffyn 1997) اما متاسفانه «شرکتهای خیلی کمی، قدرت حاصل از داشتن کارکنانی که همیشه و در هر زمان درباره بهبود کارها فکر کنند را درک کردهاند.» (MILLER, JON 2003)
جلب همکاری و مشارکت کارکنان با ....
آیا مدیری را میشناسید که نخواهد فکر و ضمیر ناخودآگاه کارمندانش در همه حال، چه در محل کار و چه در منزل، چه پشت میز کار و چه پشت فرمان اتوموبیل، به دنبال کشف عیب و نقصهای امور سازمان و ارائه راه حل برای آنها باشد؟ کدام مدیری است که نخواهد چشم تیزبین کارمندانش، غربالگر بهترینها برای سازمانش باشد؟ آیا میدانید این رویای مدیران چگونه قابل تحقق است؟ مسلما برای تحقق این خواسته، قبل از هر چیز وجود ساختار و نظامی متناسب مورد نیاز است. سیستم و نظامی که اشتیاق و انگیزه کافی را در کارکنان برای این امر بوجود آورد. آنچنان که شرح داده خواهد شد "نظام پیشنهادات" گام نخست در مسیر این تحول است سیستم مدیریتی که تاثیر قابل ملاحظه آن بر روی وجوه مختلف سازمانها از جمله رضایت شغلی، تعهد سازمانی، بهداشت روانی کارکنان و نیز بهبود بهره وری ، کیفیت و سودآوری شرکتها به عینه و در تحقیقات متعدد به اثبات رسیده است.
این سیستم که با طی مراحل فرهنگ سازی، پیشنهادگیری فردی ، پیشنهادگیری گروهی (با تشکیل گروههای بهبود مستمر یا همان گروههای QC) ، پیشنهادگیری از مشتریان و پیمانکاران و پیشنهادگیری از خانواده کارکنان به اجرا در میآید در شرکتهایی که مرتکب اشتباهاتی نظیر تاکید بیش از حد بر پاداشهای مادی، عدم فرهنگ سازی مناسب، عدم تثبیت ساختار سازمانی مورد نیاز و جانشینی مدیران نامعتقد به مشارکت کارکنان نشدهاند تحولی عظیم بوجود آورده است. برای مثال « [در سال2001] شرکت ماتسوشیتا الکتریک به ازای هر کارمند 23.7پیشنهاد دریافت کرد و ادعا کرده است که بواسطه این پیشنهادها در این سال 3000 دلار به ازای هر کارمند صرفهجویی داشته است.» (Bodek 2002، 361)
یوزو یاسودا (Yasuda)در کتابش با عنوان "40 سال، 20 میلیون ایده" (40 Years; 20 Million Ideas) (1991) اظهار میدارد تویوتا در کمتر از40 سال (از 1951 که سال شروع پیشنهادگیری در تویوتا است تا سال 1988) توانسته است20میلیون پیشنهاد برای بهبود امور از کارکنانش دریافت کند. در سالهای اخیر با مشارکت نود و پنج درصدی کارکنان تعداد پیشنهادات به 2 میلیون پیشنهاد در سال رسیده است که به معنای 40 پیشنهاد در سال به ازای هر کارمند میباشد که 96% این پیشنهادها به اجرا در میآیند. (Yuzo Yasuda 1991) بودک(Bodek) (2004) سود و صرفهجویی حاصل از اجرای این پیشنهادها را 300 میلیون دلار در سال گزارش میکند.
هنوز هم شعار تویوتا ((فکر خوب مساوی تولید خوب)) (good thinking, good product) میباشد و «بهسازی و ارائه پیشنهادات بوسیله اعضای تیمها سنگ بنیادین موفقیت تویوتا به حساب میآید.» (وب سایت رسمی شرکت تویوتا) جالب است بدانید تویوتا قبل از شروع پیشنهادگیری از کارکنان یعنی قبل از 1951 هیچ وضع خوبی نداشت و پس از اینکه 13سال از زمان تاسیساش (1937) میگذشت فقط توانسته بود 2685 خودرو تولید کند این در حالی بود که در همان زمان کارخانه فورد روزانه ???? خودرو تولید میکرد. (سقایی،????)
در سال 2004 شرکت امریکایی تکنی کالر(TechniColor) (فعال در حوزه تولید، تکثیر و توزیع فیلم و محصولات سرگرمی) با1800 کارمند، 22000 پیشنهاد دریافت کرد که بیش از 12000عدد از آنها به اجرا در آمدند و در عرض یک سال 10میلیون دلار برای این شرکت سود و صرفهجویی حاصل کردند. (&Bodek Chuck 2005، 209)
ماساکی ایمایی در کتاب "کایزن، کلید موفقیت رقابتی ژاپن" (ترجمه صحیح آن "بهبود مستمر، کلید موفقیت ژاپن در رقابت [جهانی]" است) می نویسد: « آیا می توانید به نوعی سرمایه گذاری فکر کنید که سالانه 500درصد بازدهی سرمایه داشته باشد؟ آن هم از نوعی که به آغاز یک فعالیت اقتصادی جدید و یا تولید محصولی جدید نیاز ندارد؟ ظاهرا مدیران شرکت نیسان کمیکال به چنین سرمایه ای درست یافته اند: فعالیت گروه های کوچک نظام پیشنهادها. آنها از سال 1978 یک سیستم پیشنهادات را در سطح شرکت بر اساس فعالیت این گروه ها بکار گرفته اند و سرمایه گذاری کل 200 میلیون ینی آنها منجر به کاهش هزینه به مبلغ یک میلیارد ین شده است.»
نظام پیشنهادها با بوجود آوردن فرصت رفع نیاز کارکنان به احترام، خودیابی، آزادی بیان و برابری، به علاوه توجه بیشتر به مشکلات کارکنان و کاهش مشکلات کاری ایشان با اجرای پیشنهادها و نیز با اعطای پاداشهای مادی و احترامات عالی، باعث افزایش رضایت شغلی و احساس تعلق و نزدیکی بین کارکنان و سازمان میشود. نتیجه این حس نزدیکی، تلاش متقابل کارکنان برای رفع مسائل سازمانشان خواهد بود. شاهد این گفته تحقیقات دانشگاهی متعددی است که تاثیر مثبت نظام پیشنهادها بر رضایت شغلی کارکنان را تایید میکند برای مثال تحقیق حبیبی(1383) نشان میدهد که بین نظام پیشنهادها و رضایت شغلی کارکنان و نیز انگیزش کارکنان در حوزه ستادی سازمان بازرسی و نظارت بر قیمت و توزیع کالا و خدمات رابطه مثبت معناداری وجود دارد. همینطور در تحقیقات کریمی (1378) در شرکت برق منطقهای فارس وجود رابطه معنیدار و مثبت بین اجرای نظام پیشنهادها و رضایت شغلی کارکنان به اثبات میرسد. تحقیقات اورین(Orin) (1991) در صنایع خدماتی کلورادو امریکا نیز نشان میدهد با اجرای تکنیکهای تصمیمگیری مشارکتی میزان بهرهوری و رضایت شغلی کارکنان صنایع افزایش مییابد. (حبیبی1383)
اما این حس تعلق و نزدیکی کارکنان به سازمانشان تا آنجا میتواند پیش رود که کارمندان ژاپنی اغلب خود را با نام سازمان محل کارشام معرفی می کنند! عواید چنین نزدیکی متقابلی بین کارکنان و مدیران، بیش از آن چیزی است که در ابتدا به نظر میرسد آنچنان که تویوتا در شوک افزایش قیمت نفت به سال 1973 که بواسطه افزایش هزینه های تولید و کاهش فروش، ناگزیر به اخراج کارکنان برای کاهش ظرفیت تولید و هزینههای سربار بود، هیچ کارمندی را اخراج نکرد بلکه از کارکنانش درخواست کرد با همدلی و همراهی برای کاهش هزینههای تولید پیشنهادهای بیشتری ارائه دهند. کارکنان نیز این درخواست را با جان دل شنیدند و با تلاش فکری مضاعف، سرانه پیشنهاد را از 2-3 پیشنهاد در سال به 12 پیشنهاد در آن سال افزایش دادند. به این ترتیب تویوتا توانست با کاهش هزینهها از بحران نجات یابد تا امروز که به عنوان سوددهترین (فورچون، مارچ2007) و بزرگترین خودروساز در جهان (با 192میلیارد دلار سرمایه بازار) فراتر از دایملر-کرایسلر (با89 میلیارد دلار سرمایه)، هوندا(62 میلیارد دلار) و فولکس واگن(57میلیارد دلار) قرار گرفته است. (رویترز، می2007) جالب است بدانید بیش از 50 سال است که تویوتا تحت هیچ شرایطی هیچ کارمندی را اخراج نکرده است. (رابینسون و شرودر 2004،110) «وقتی در کارخانه[واحد کنتاکی تویوتا] قدم میزنید رضایت و خشنودی را در چهره کارکنان و نحوه کارکردن ایشان میبینید. »( Turner 2002)
«دیوار ژاپن» ساخته شده با مصالحی از جنس تفکر و خلاقیت:
مجتبی کاشانی (1382، 114)یکی از مدیران اجرایی کشور با بیان خاطره بازدیدش از یک کارخانه ژاپنی تولید کلاچ اتوموبیل در سال 1987 از ساخت «دیوار ژاپن» در این کارخانه صحبت به میان میآورد. دیواری که برخلاف «دیوار چین» نه بر اساس ظلم و استبداد بلکه براساس اندیشههای شکوهمند کارکنان بوجود آمده است: «در حین مشاهده و بازدید از عجایب گوناگون در سالن تولید این کارخانه، متوجه یکی از دیوارهای این سالن به طول حدود 50 متر و ارتفاع 8 متر شدم که تمامی سطح آن از کاغذهای پرنوشته ای پوشانیده شده بود. کنجکاوی مرا به سوال وادار کرد. در پاسخ دریافتم که این کاغذها پیشنهادهای کارکنان این واحد برای تبدیل تولید آن به CAD/CAM (ساخت به کمک کامپیوتر /طراحی به کمک کامپیوتر) میباشد و هر یک از کارکنان به طور متوسط 11 پیشنهاد کتبی داده است. مدیریت نیز چون موفقیت در اجرای این طرح را مدیون پیشنهادهای کارکنان در همه سطوح میداند برای تشویق و اشاعه سیستم مدیریت مشارکتی و نظام پیشنهادات، بزرگترین دیوار طولی این سالن را با اندیشه آنان آراسته است. میگفتند این کار هم به ما و هم به آنها انرژی، دلگرمی، انگیزه و سرفرازی میدهد...»
در واقع بر اساس همین مشاهدات است که محققان بسیاری نظام پیشنهادها را به عنوان نظام و ابزار اصلی برای بهبود مستمر و هسته اصلی همه سیستمهای برتر کیفیت و بهرهوری معرفی میکنند:
ترنر(2002) اظهار میدارد « احتمالا قبل از پروژه شش سیگما(Six sigma) بعدی، شما باید یک برنامه نظام پیشنهادها را مورد توجه قرار داده و اجرا کنید »
به عقیده میلر(Miller) «تولید ناب یک تفکر در کسب و کار است که همه را به بهبود روزانه متعهد میسازد.... یکی از ابزارهای تولید ناب که به طرز خیلی بدی درک و به کار گرفته شده نظام پیشنهادات است.»
لوئیس آرویو مدیر مهندسی تولید پیشرفته شرکت سنسورماتیک، برنده جایزه شینگو (Shingo prize) برای تعالی در تولید که اخیرا شرکت متبوعش بواسطه پیشنهادات1200 کارمند شرکت 1.7میلیون دلار صرفهجویی داشته معتقد است: «نظام پیشنهادها یک عنصر حیاتی و مهم در کمک به ما در اجرای تولید ناب میباشد. نظام پیشنهادها انجام کارهای اساسی را برای ما آسانتر میکند.» (Productivity Press Development Team 2005،33)
بدون شک «نظام پیشنهادها یک عنصر اصلی برای همه سازمانهایی است که به طور مستمر در حال بهبود میباشند.» (Schuring& Luijten 2001)
«هم اکنون در ژاپن 91.7 درصد از موسسات ثبت شده در بورس توکیو نظام پیشنهادها را اجرا میکنند. طبق قانون اداری امریکا تمام موسسات دولتی، بودجه و تشکیلات خاصی برای اجرای نظام پیشنهادها دارند و همه ساله بهترین پیشنهاددهنده از دست رئیس جمهور امریکا لوح تقدیر و جوایزی را دریافت میکند.» (حبیبی 1383) البته خوشبختانه اخیرا بر اساس مصوبه مجلس[2] اجرای نظام پیشنهادها برای کلیه دستگاههای اجرایی الزامی گشته است.
نتیجه گیری:
"بهبود مستمر تمامی امور سازمان" کلید دستیابی به کیفیت و بهرهوری برتر میباشد و این امر میسر نمیشود مگر با جلب مشارکت تمامی کارکنان. موثرترین سیستم شناخته شده برای جلب مشارکت کارکنان و سایر افراد مرتبط با سازمان، "نظام پیشنهادها" میباشد که با اجرای صحیح آن، اولین و مهمترین گام در مسیر دستیابی به سیستمهای برتر کیفیت و بهرهوری برداشته شده است و بدون آن، کیفیت و بهرهوری متعالی معنایی پیدا نخواهد کرد. سیستمی که براساس گزارش «انجمن مشارکت کارکنان»(EIA: employee involvement association) 4 تا10برابر مجموع هزینههای اجرایی و پاداشهای اعطایی، سود و صرفهجویی به ارمغان میآورد. این انجمن تخمین میزند که میانگین صرفهجویی خالص از اجرای این سیستم به ازای هر کارمند، مقدار افسانهای 1360دلار در سال میباشد.» آیا از سرمایهگذاری برای بکارگیری فکر و ذهن انسانها غیر از این میتوان انتظار داشت؟
منابع:
? حبیبی، لیلی (1383) ، بررسی و تجزیه و تحلیل رابطه بین نظام مدیریت مشارکتی (با تاکید بر سیستم پیشنهادها) و اثربخشی کارکنان سازمان بازرسی و نظارت، پایان نامه کارشناسی ارشد، دانشکده مدیریت دانشگاه تهران
? رویترز، نقل در روزنامه آفتاب، (3 خرداد1386) ،" تویوتا بزرگترین شرکت خودروسازی در جهان شناخته شد" صفحه اقتصادی
? سقایی، عباس –عظیمزاد، نیما(1385)، بکارگیری تولید ناب به عنوان چارچوبی برای بهبود سازمانها، مجله گسترش صنعت، شماره دى ماه
? کاشانی، مجتبی (1382) ، نقش دل در مدیریت، چاپ دوم، انتشارات سازمان مدیریت صنعتی
? کریمی، حمیدرضا (1378)،" بررسی تاثیر اجرای نظام مدیریت مشارکتی از طریق سیستم پیشنهادهای کارکنان بر افزایش بهرهوری در شرکت برق منطقهای فارس"، پایان نامه کارشناسی ارشد به راهنمائی: علینقی مصلحشیرازی، دانشگاه شیراز.
? ایمایی، ماساکی (1372) "کایزن-کلید موفقیت رقابتی ژاپن"، ترجمه محمد حسن سلیمی، انتشارات دانشگاه امیر کبیر
? Bessant, John & Caffyn, Sarah, (1997) “High-involvement innovation through continuous improvement”, International Journal of Technology Management, Volume 14, Number 1, Pages: 7 - 28
? Bodek, Norman, (2004),”The Power and Magic of Lean”, PCS Press
? Bodek, Norman & Yorke, Chuck, (2005 (”All You Gotta Do is Ask “, Published by PCS Inc.
? Cheng, T.C. & Podolsky, S. (1996),” Just-in-Time Manufacturing: An introduction”, springer publication
? FORTUNE Magazine (March2007),”America"s best car company”, Alex Taylor III
? Herriot, Peter & Stickland, Rob (1997) “The Management of Careers”, Psychology Press
? MILLER, JON, (2003) “The suggestion system is No suggestion”, Gemba Research, November.
? Patel, M. K. (2005), “Case studies on HRD practices”, Published by Anmol Publications PVT. LTD, ISBN: 81-261-2150-5
? Productivity Press Development Team, (2005) “Lean Culture: Collected Practices and Cases”, Productivity Press, ISBN: 978-1-56327-326-1
? Robinson, Alan G. & Schroeder Dean M. (2004) “Ideas Are Free: How the Idea Revolution Is Liberating People and Transforming Organizations”, Barrett-Koehler Publishers, ISBN: 1576752828.
? Schuring, Roel W. & Luijten, Harald, (2001), “Reinventing suggestion systems for continuous improvement”, International Journal of Technology Management, Volume 22, Number 4, Pages: 359 – 372
? Shingo, Shigeo & Dillon Andrew P. (1989), “A Study of the Toyota Production System: From an Industrial Engineering [view]point” , Published by Productivity Press
? Turner, Freda, (2002)” An Effective Employee Suggestion Program Has a Multiplier Effect”, Refresher publications.
? Yasuda, Yuzo, (1991) "40 Years, 20 Million Ideas: The Toyota Suggestion System", Translated by Fredrich Czupryna, Cambridge, MA, Productivity Press, Inc.
Abstract in English:
There is an arrangement in implementing productivity & quality improvement systems. Having no attention to this arrangement will cause multiple problems for organization but no improvement.
The first & most important step towards excellence in quality & productivity (as it has seen in history of quality movement and according to quality masters) is involving all the employees in continuous improvement. Continuous improvement in all levels of organization can not be achieved without establishing a comprehensive system for it and the system is employee suggestion system. Corporations that set up effective suggestion systems are finding that employees have great ideas that can lower costs, increase revenues, improve efficiency or make greater quality.
Keywords: excellence in quality & productivity, continuous improvement, JIT, lean thinking, suggestions system


یک نظر اضافه کنید
شماره موبایل شما منتشر نخواهد شد.زمینه های مورد نیاز هستند علامت گذاری شده *
امتیاز شما